Projects awarded to TAKRAF reinforce the brand’s reputation as a world-leading technology and full-service supplier of bulk material handling systems, from designing safe and environmentally-friendly installations that maximize productivity, to providing customized maintenance, upgrade and refurbishment solutions that optimize both safety and efficiency.
“Just as operational efficiency is a focus area in TAKRAF’s approach to bulk material handling, achieving such efficiency with increased safety and minimizing environmental impact is a non-negotiable,” says Thomas Jabs, TAKRAF Group CEO. “As we have shown, both in the development of our technology and of our maintenance solutions, there is no need for one to be at the expense of the other.”
Technology Milestones
TAKRAF continues to establish industry milestones in the engineering of customized solutions for its global client base. For example, a TAKRAF rail-mounted stacker at an Australian bulk terminal is one of the largest and most technically advanced, featuring:
- Initial stacking capacity of 6,300 t/h
- 62 m long curved boom
- Ability to accommodate a peak volumetric rate of up to 10,700 m³/h (9,600 t/h)
Six patents resulted from the design of the world’s most powerful belt conveyor system for a Chilean copper miner, boasting a capacity of 11,000 t/h:
- Total installed drive power of 58 MW
- Two underground conveyors (totaling more than 6.3 km in length) with 10,000 kW of installed drive power per drive pulley and 20,000 kW per conveyor
- More than 5.3 km-long overland conveyor with three 5,000 kW direct drive motors
Gearless drives on the underground and overland conveyors significantly reduce the main wear parts and the drive system’s footprint. Furthermore, such efficient electric drives result in CO2 emissions being reduced by around two-thirds as compared to trucks for the same copper volume.
Other recent projects in South America include a 13,200 t/h belt conveyor system and a 7,200 t/h bucket-wheel reclaimer, while TAKRAF replaced, in just 3 days, a 6,000 t/h rail-mounted stacker in south Mexico.
The high dynamic loads and forces resulting from the passage of trains presented a major challenge in the engineering of a greenfield wagon unloading station, constructed entirely from steel, for Phase 1 of a bauxite expansion project in Guinea, Africa. The contract also included supply of:
- Primary and secondary crushing stations
- A complex brownfield conveyor system, with a further two conveyors being ordered subsequently
- Four portal scraper reclaimers for a Japanese multi-commodity warehouse are some of the largest built and feature a safety and anti-collision system, as two reclaimers are required to work on the same rail in the same warehouse.
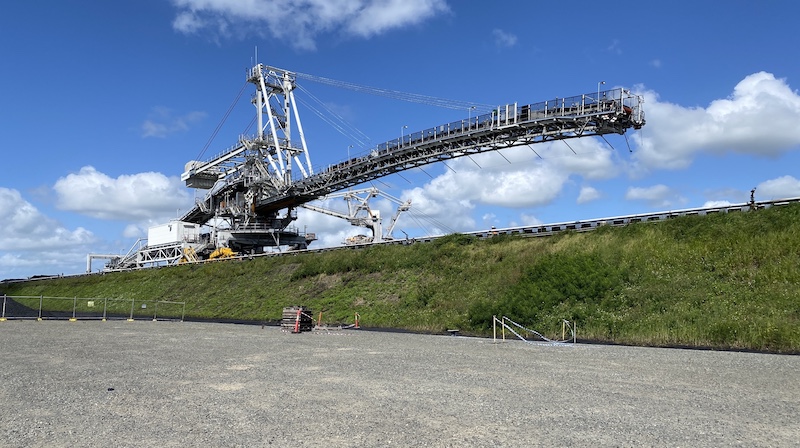
TAKRAF’s impressively long-boomed stacker ready to be put into operation at the bulk terminal in Queensland, Australia.
Intelligent Maintenance
TAKRAF’sintelligent approach to chute liner replacement highlights its holistic thinking on maintenance. Embracing a holistic maintenance philosophy eliminates the need for compromises, ensuring that both safety and efficiency do not need to come at the expense of the other. While one method of reducing accidents during chute liner replacement is to design chutes with modular sections, the safest approach is of course to stay outside of the chute completely. As a result, TAKRAF’s developments include external access for both the lip liner and wear plates, and ultrasonic measurement of liner thickness, and wear, from outside the chute. This also means reduced downtime, as scaffolding is not required.
TAKRAF’s maintenance cart has made a significant impact on safety and efficiency when replacing worn or damaged rolls (idlers) on long overland conveyors, especially on steep slopes, tunnels and on elevated structures. The cart can access any location along a conveyor belt in the shortest possible time and in the safest manner. In North America, a TAKRAF maintenance cart services the steep, 26 % decline section of a 4,350 m overland conveyor, which boasts more than 3,700 rolls over a 1,250 m length. A TAKRAF maintenance cart was also of interest for a South American copper mine due to the increased safety it would provide during the difficult maintenance of its complex, 6,000 m-long overland conveyor.
Innovation out of tradition – It pays to talk to a specialist!
About TAKRAF Group
TAKRAF Group, through its established and well-known brands, TAKRAF and DELKOR, provides innovative technological solutions to the mining and associated industries. With experience acquired over more than a century, the Group is well positioned to provide equipment, systems and services that best satisfy its clients’ mining, comminution, material handling, liquid/solid separation and beneficiation requirements. Servicing owners and operators around the world, TAKRAF Group‘s engineered solutions are customized to the unique project requirements and are aimed at lowering the total cost of ownership and reducing environmental impact by improving efficiency with safe and reliable equipment.
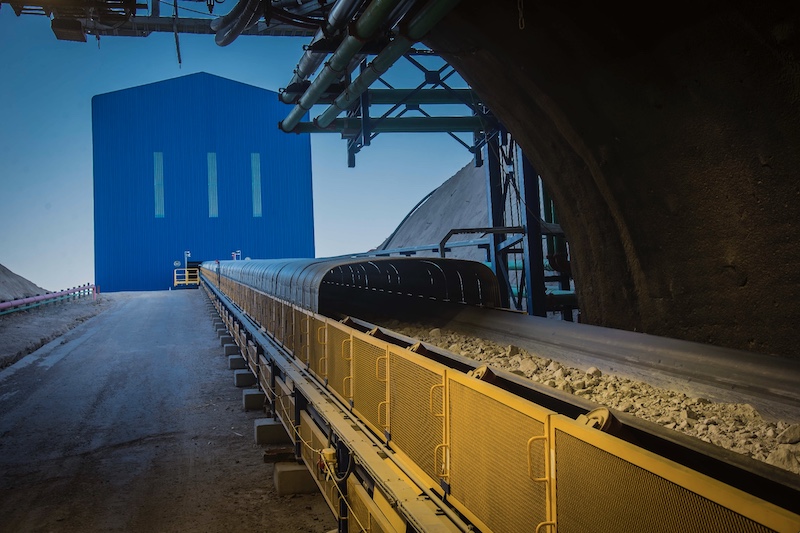
The world´s most powerful belt conveyor system in Chile featuring gearless conveyor drive technology.
For further information, visit www.takraf.com or, e-mail info@takraf.com.